State of the Art Stone Wool Equipment
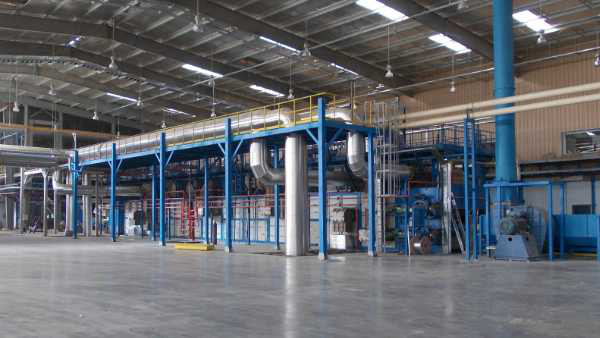
STONE WOOL EQUIPMENT
FinMach GmbH supplies State of the Art Stone Wool Equipment, having standards widths of 1.200 mm and 2.400 mm. FinMach also offers modifications and upgrades of existing Rock Wool Production Lines, supplying high performance machineries and advanced process technologies to improve production capacity and products quality.
FinMach supplies completely automatic Raw Materials Plants / Batch Plants to load the melting furnace with the raw materials in the correct quantity, ratio, size, and mixing.
The offered melting furnaces are:
- the Coke Cupola, the most common furnace in use for melting the basalt mixes.
- the Gas Cupola, to be installed wherever the natural gas availability and price are competitive.
- the Electric Melter to be installed when a compliance with the strictest CO2 emission levels is required.
The lava, produced in the correct temperature and viscosity, is processed with the spinners the so-called fiberizing machines, which are equipped with 4 high speed spinning wheels and with an advanced binder distribution system. The spinners are designed to produce fibers with the required dimensions, thicknesses, and shots contents to obtain high quality Stone Wool Products.
The produced fibers are collected onto a drum type Fiber Collecting Chamber, equipped with a high-pressure water cleaning system (automatic), a net drying system and a shots separation system. The Fiber Collecting Chamber is connected to a well-designed suction system, with an increased suction efficiency that reduces to the minimum the fiber wastes.
The collected fibers are distributed on the Mineral Wool Production Lines by means of a pendulum and conveyed into the Crimping Machine to obtain the fiber orientation and then into a high efficiency and well insulated Curing Oven, that cures the binder and forms the Stone Wool products in thickness and density.
The products, once out of the Curing Oven are cooled and cut longitudinally by means of a Longitudinal Cutting Machine, equipped with dustless disks, that reduce material waste and dust. The Rock Wool products are then cut transversally into length by a high precision Cross Cutting Machine. This machine cuts the products on the fly (Flying Cutting Machine) and performs a clean cut.
The produced boards are conveyed into a Rock Wool Stacking Machine, and the boards piles are packed my means of a Rock Wool Packing Machine.
The mats are either conveyed into a Stitching Lines, equipped with the most advanced Stitching machines, or directly into Roll-up machines, that Roll and Pack the mats automatically, without any human intervention.
Consolidated Rock Wool Production Process Technologies, through advanced Equipment and Process Automation Systems, are implemented into each production line.
All gasses produced in the melting and the curing process are collected and conveyed into Exhaust Gasses Cleaning Systems where the dust particles are collected and safely stored, and the pollutants are reduced to permissible levels according to the most restrictive emission regulation.
FinMach Team, thanks to deep knowledge of processes and equipment, develops customized solutions that fit into the case-by-case needs of the customers to improve lines’ performance in terms of productivity, transformation costs and product quality, during the full line life cycle.
See Also: Stone Wool Equipment, Stone Wool Lines, Stone Wool Plants, Stone Wool Production Lines by Finmach.